
WEEK- 4​ Oct - 12
QUALITY CONTROL
Quality measures that we observed:
​
-
To ensure the highest quality of concrete, they have hired a consultancy called ‘Nova Engineering and Environmental, Atlanta’ for performing cylinder test on Concrete.
​
-
As stairs act as an ‘Emergency Exit’ at the time of fire hazard, they are taking extreme cautions to make the stair walls fire proof. The quality in the work is maintained in such a way that the stair walls can withstand a continuous fire for 3 hours without failing. To achieve that, they are using a material called ‘DensGlass – A fiberglass mat gypsum sheet.
​
​
​
​
​
​
​
​
​
​
​
-
Quality on MEP work: Every intersection of pipeline and floor at each level of building is provided with foam insulation to improve the durability of plumbing system.
​
-
To achieve superior quality of concrete finishing, each part of formwork is applied with oil coating. This will help to achieve :
-
Honeycomb free concreting.
-
Easy removal of formwork.
-
Smooth exterior surface.
-
Some properties of DensGlass:
-
Superior moisture and mold resistance.
-
A rigid substrate for a wide variety of air or water-resistive barrier systems.
-
Flexibility with construction schedules despite of bad weather.

Quality Control that we witnessed:
​
-
When our on-site advisor Mr. Victor Martinez was explaining us the MEP work system on Ninth Floor, he caught one mistake in placing of fire water pipe and he showed us how they report any mistake found during routine quality inspection.
-
For reporting any modifications or mistakes in construction, they use software called, Procore - Quality and Safety.

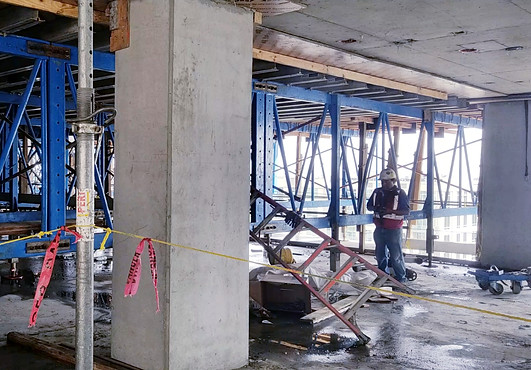
24th Floor: They have divided the floor into 2 sections. In this week, they have completed the concrete work of section 1. And section 2 formwork installation was in final stage.
23rd Floor: Steel framework removal and shifting to the next floor was in process.
22nd Floor: Construction of story entrance for temporary elevator was completed. Exterior glass installation was ongoing,
21st and 20th Floor: This week, they have completed installation of exterior glass frame. Along with that, staircase roofing construction was in process.
19th and 18th Floor: Floors was getting ready for the piping layout. They were using Shop back vacuum pump for floor cleaning. Exterior water proof painting was simultaneously performed at the time of our visit.
17th and 16th Floor: Interior wall steel framing was almost 30% completed and Dry wall framing for staircase was just started.
15th, 14th and 13th Floor: MEP layout and HVAC installation around the interior frame was in process.
12th and 11th Floor: MEP installation was completed and along with duct pipe, they were installing the sprinkler system for fire protection.
10th, 9th and 8th Floor: Electric wiring on the one side of the floor 9 was completed and work for courtyard entrance from floor 8 was in process.
Below 7th Floor: They have successfully passed the Inspection of MEP, electric and plumbing work. On floor 5, insulation for staircase was in process. They have started installation of tiles in the bathrooms of floor 2. AT&T wifi installation was completed.
​
QUALITY CONTROL
FLOOR PROGRESS